近日,全球首台165米级预应力钢管混凝土格构式塔架在山东德州乐陵市成功完成安装,扎根于齐鲁大地,送电至千户万家。该塔架的风电机组预计每年产生超过1240万千瓦时清洁电力,节约标煤约0.4万吨,减少碳排放约1.2万吨。该新型高塔结构凝聚了重庆大学周绪红院士和王宇航教授团队5年的心血,解决了我国陆上低风速区风资源开发中的“卡脖子”问题,打破了国外在风电机组高塔结构领域的垄断,促进了我国陆上风资源的高效利用,推动了我国风电工程技术发展。
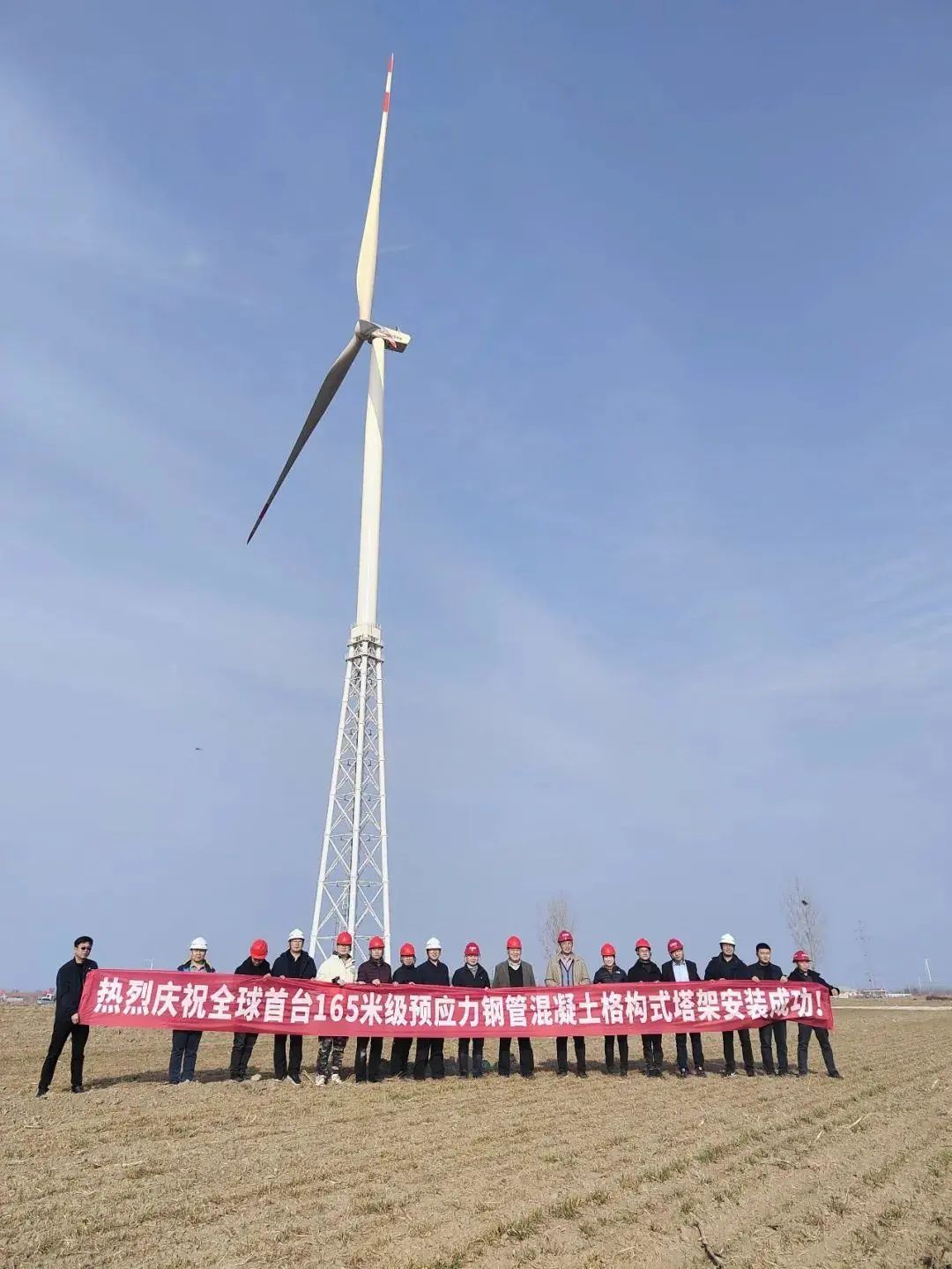
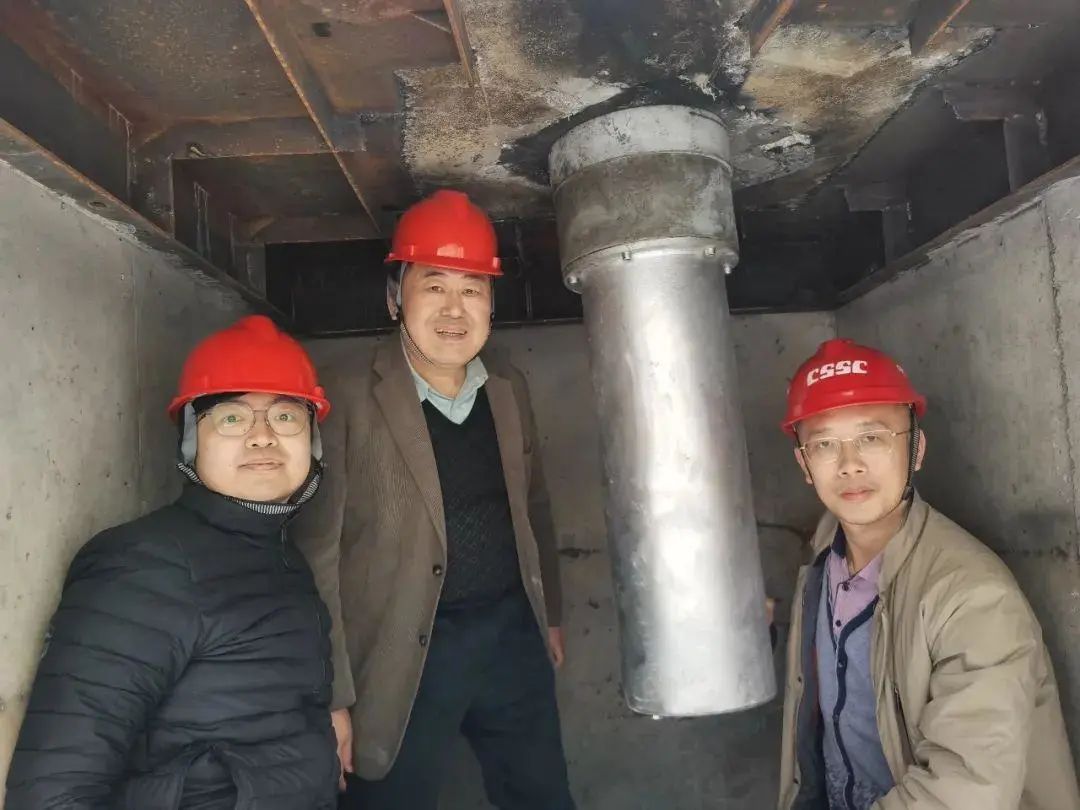
“目前,我国陆上风电面临单机容量不断增大、轮毂高度显著提升、叶片长度持续增加等趋势,塔架结构是保障风电机组安全运行的关键。风电机组的轮毂高度超过160米后,传统塔架结构尺寸和重量大、综合成本高,已难以适用。” 著名结构工程专家,中国工程院院士,风电工程结构团队执行负责人周绪红院士、重庆大学土木工程学院副院长王宇航教授带领团队从塔筒结构的性能、尺寸限制、成本控制三个维度出发,于2018年原创提出了这种新型结构,并获得了国家专利。2020年底,在周绪红的指导下,团队建立了预应力钢管混凝土格构式塔架结构精细化高效分析理论和计算方法,并于2021年与中国船舶集团海装风电股份有限公司联合开展示范工程的实施。
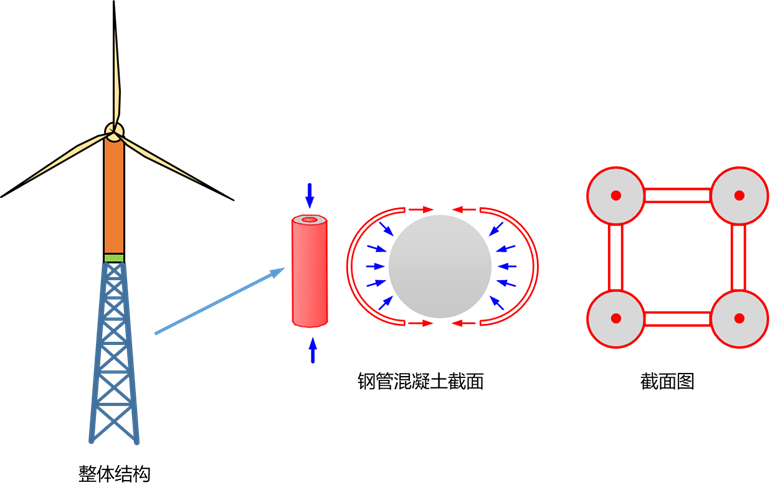
然而高塔直立并非易事,该结构受力复杂、无相应的设计规范可参考、无成熟的国内外经验可借鉴。研发团队在其诞生之时就面临着重重技术难关:如何提出一整套完善的分析理论与高效的设计方法?如何可靠连接下部格构段与上部钢塔段?如何保证格构式塔架节点的抗疲劳性能?如何实现钢管混凝土格构式塔架的快速预制和模块化安装以提高生产与安装效率?
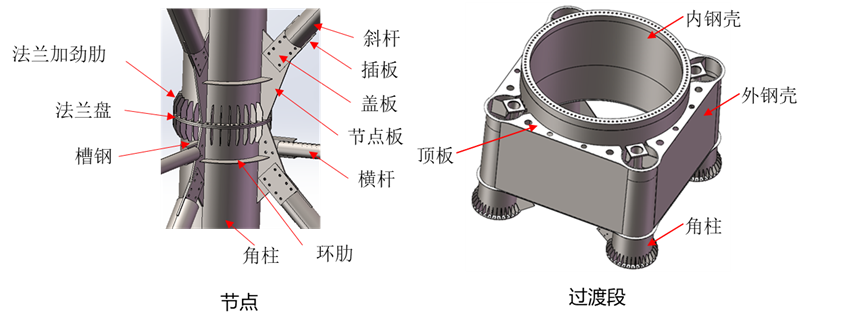
在预应力钢管混凝土格构式塔架的开发过程中,为了解决这些技术性难题,保证结构各个部位的性能都能发挥其最好的效果,团队成员不断地与业内专家进行技术交流与探索,不断地对结构受力性能进行分析与测试、不断地对方案进行改进与优化。因此,在一次次开会讨论、一次次修改方案、一次次推翻重来后,攻克了研发设计、仿真模拟、试验测试及理论分析中的难关险阻,经历了20余次的反复选型、模拟迭代、受力分析,综合考虑制造成本、运输限制、加工难度、质量把控难度、安装难度等各种因素后,团队最终从100余套方案中确定了综合指标最优的结构初步方案。
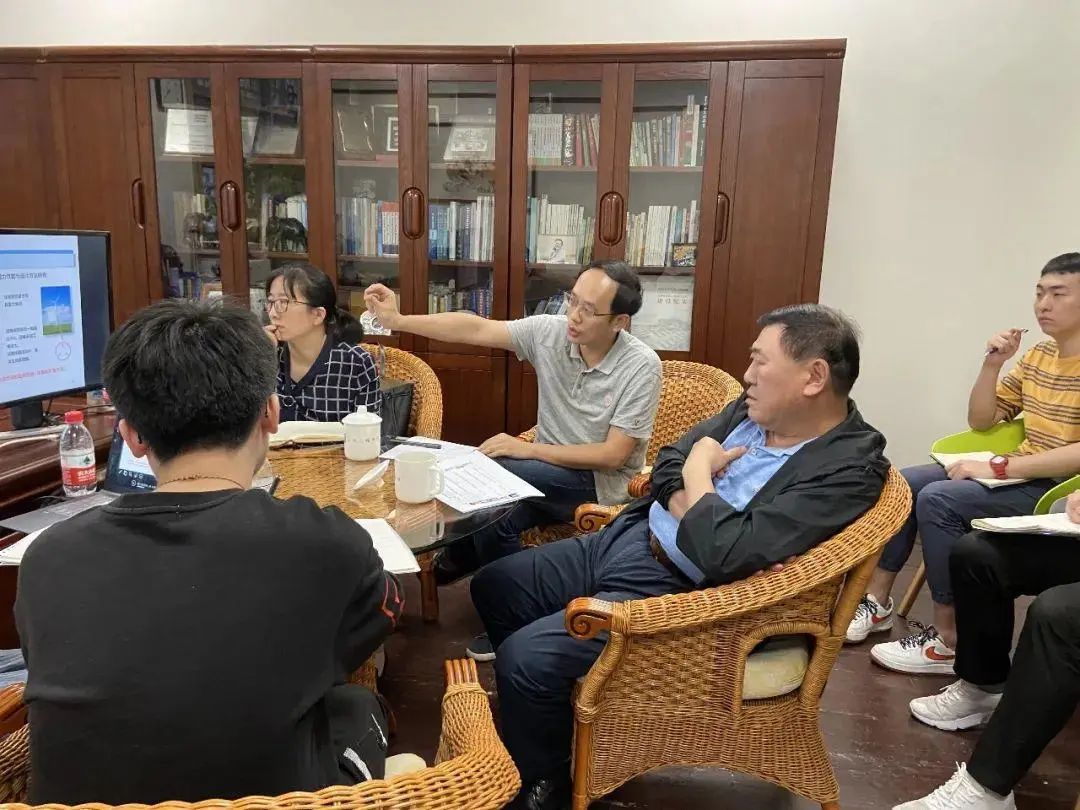
“尽管在这个过程中做了些无用功,但所有路都不是白走的,一项新的研究成果能被大家认可和采纳,都要有一个这样的过程。”在团队成员遭受挫败时,周绪红院士这样勉励的话语再一次激发起大家的斗志。王宇航教授也经常以周绪红院士的科学家精神激励大家,通过这种大的创新、大的突破、大的项目激发团队成员的责任感、使命感、科研的幸福感,培养大家攻坚克难的勇气和不懈探索的精神。
七八月份的重庆异常炎热,项目也在这时进入了紧张的最终设计阶段,各方需要保持时刻沟通,为了更高效的工作,团队博士研究生王康、胡超、李琦琦、刘宇森等一起进驻到中国船舶集团海装风电股份有限公司进行集中办公,每天往返于公司与学校间,克服了一个又一个难点,对每个部分都将细节扣到极致,所有的设计方案都做到有据可依,最终完成了塔架的整体结构设计,并顺利通过了认证。
2021年11月,研发设计工作圆满结束,团队成员还顾不上欣喜就立即投身于样机示范工程中去。为了保证塔架顺利安全地生产,团队成员都始终奋战在第一线,精心雕琢着全球第一台预应力钢管混凝土格构式塔架。
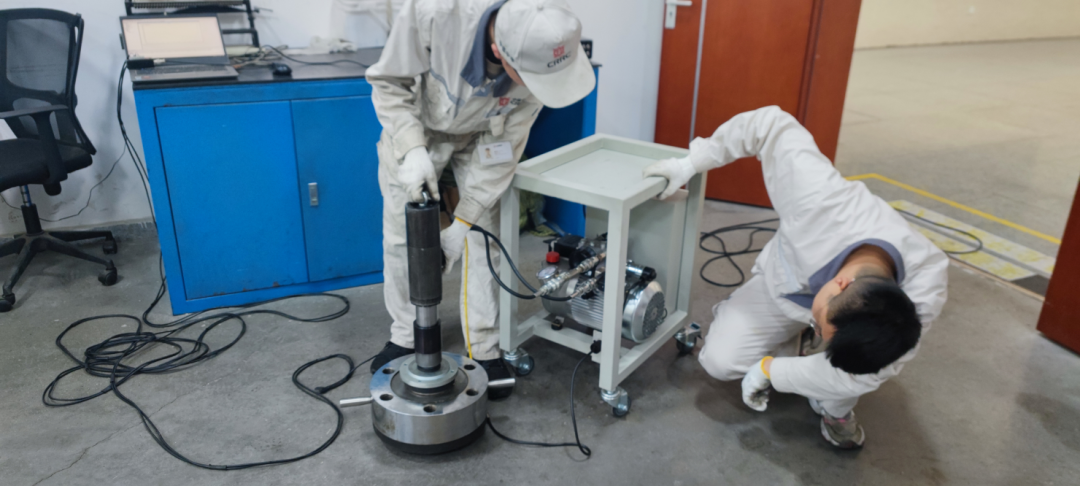
为了一颗螺栓的安全,团队对各种类型螺栓进行测试,在眉山中车紧固件科技有限公司进行历时三个月的调研,最终确定采用防松性能优异的环槽铆钉连接技术,确保结构连接处的安全。
为了寻找合适的生产加工厂家,团队多次前往山东青岛胶州,进行不同生产厂家的实地调研,与生产厂家进行生产工艺、质量监控方案、优化设计方案等技术交流。
为了保证机位点的吊装精度,团队对每一个节点坐标都进行了测量,对每一根杆件进行了编号,建立了塔架各关键节点数据库,充分掌握吊装过程中可能遇到的问题,并提前给出解决方案。
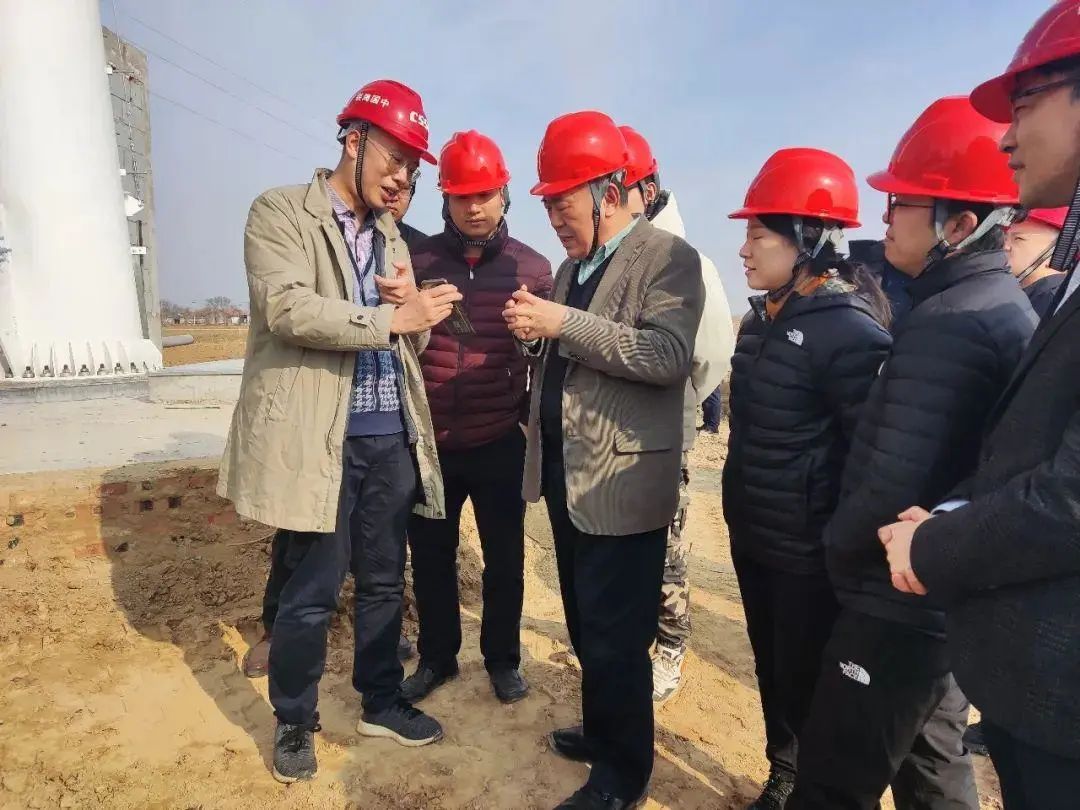
2022年12月样机工程的塔架开始正式组装,此时正值全国疫情高峰期,构件运输及现场作业等都受到疫情影响,各单位之间通过紧锣密鼓的安排、部署、再部署,所有人员发扬万众一心、团结互助、同舟共济、迎难而上的精神,最终在2023年春节来临之前将样机工程顺利安装。
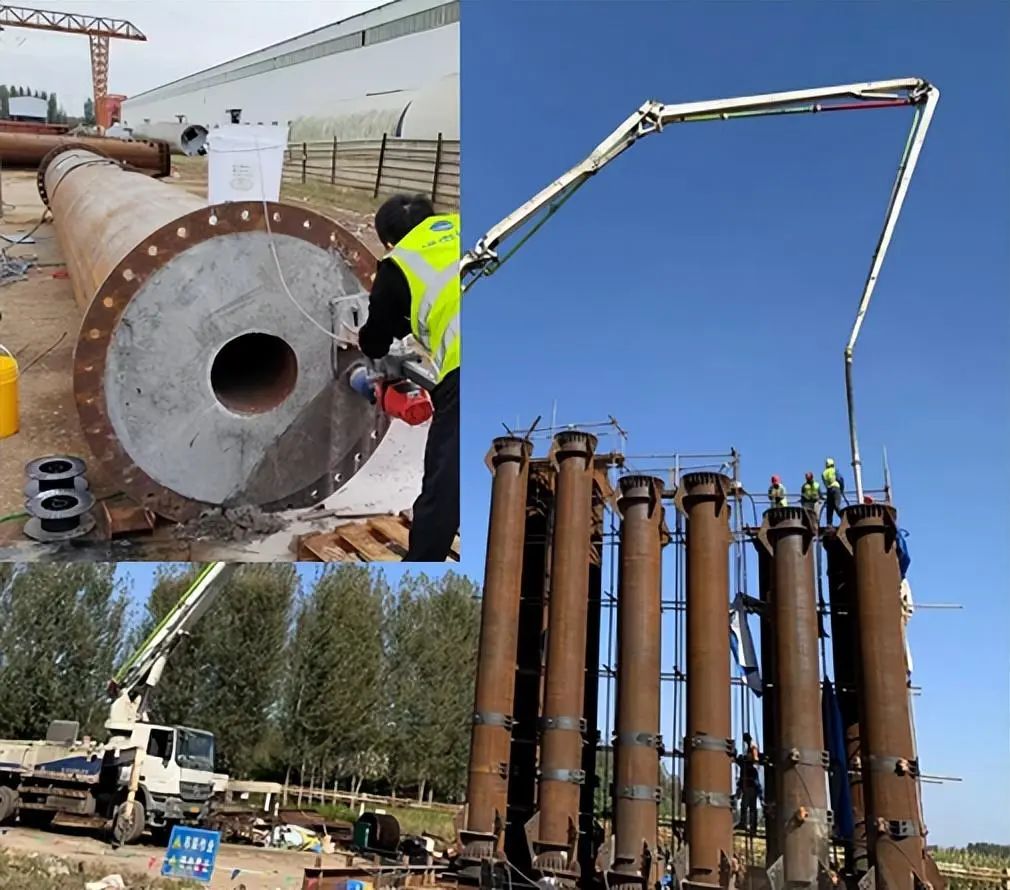
正如周绪红院士所说:“所有光鲜亮丽的背后,都熬过了无数个不为人知的黑夜”。项目团队成员勇担重任、迎难而上、密切协作,发扬拼搏精神,最终成功完成了这件“大国重器”。未来,团队将进一步开展海上风电固定式支撑结构与漂浮式基础结构体系研发,并建立一体化分析理论与设计方法,突破关键理论与技术瓶颈,进一步推动钢-混凝土组合结构与混合结构在风电工程中的应用,助力我国风电产业从陆地走向海洋、从近浅海迈向深远海,为我国清洁能源发展与“双碳”目标的实现作出贡献。
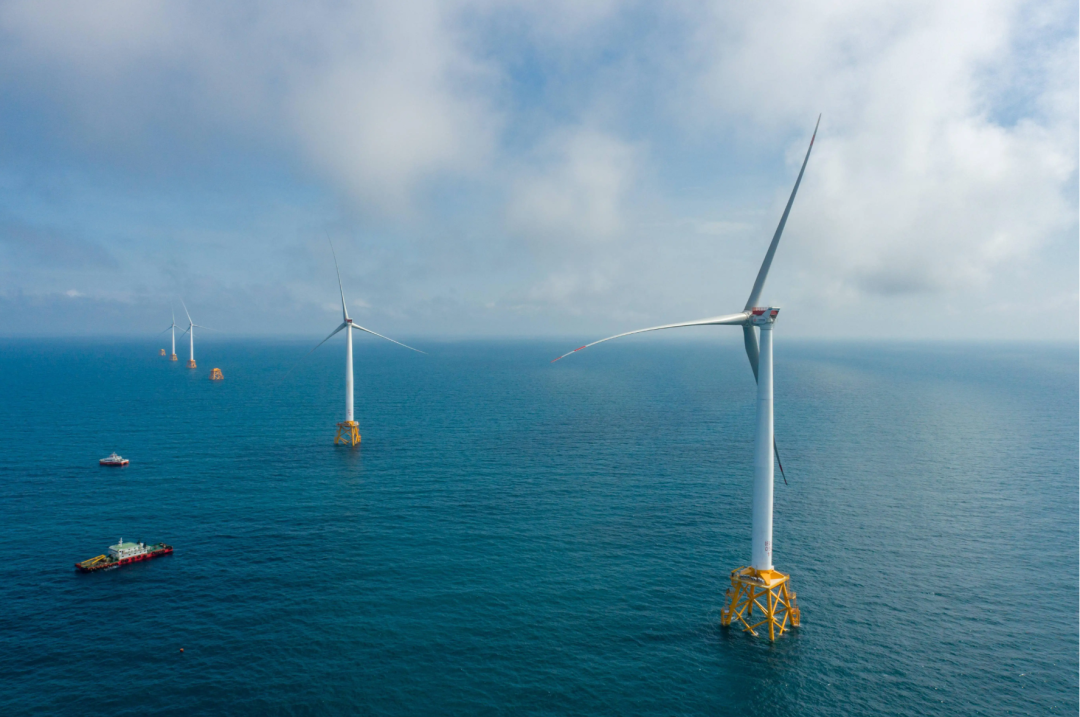

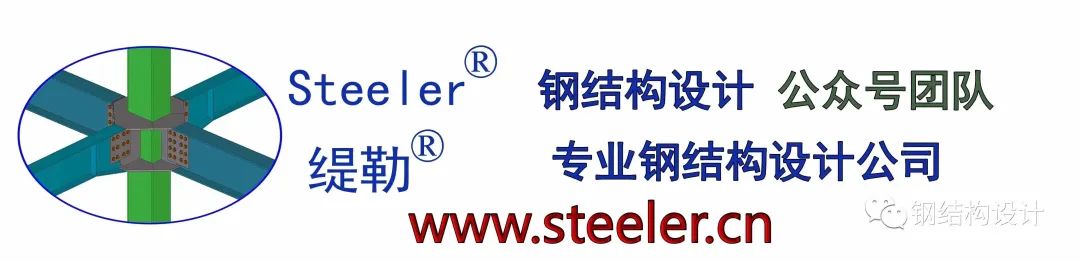
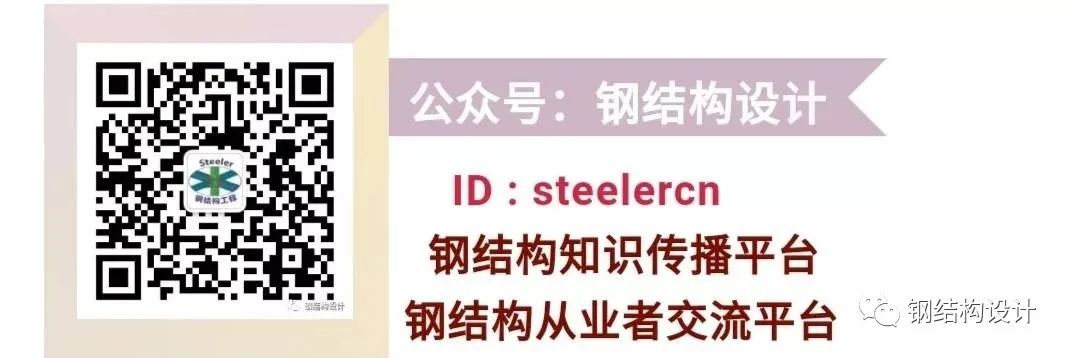
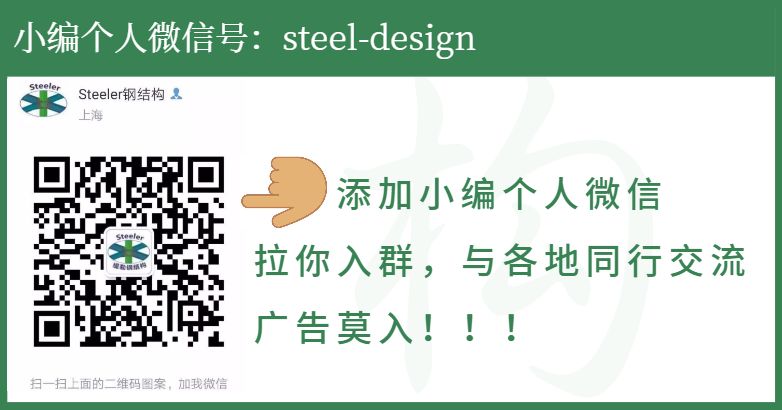


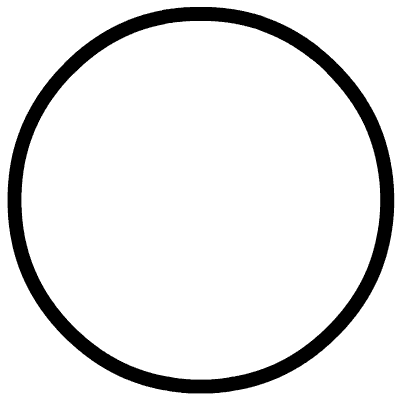