南京一中江北校区(高中部)按照“国际知名、国内一流”的定位标准建设一所14轨制42班的高标准寄宿制高中,作为未来南京一中高中部。校区占地面积150亩,总建筑面积107728㎡,内部被一条城市道路分为东西两个地块,教学组团分布在西侧地块,生活运动区分布在东侧地块,中间通过下沉通道将校园连接为一个整体。
南京一中江北校区项目由中建科技集团有限公司以设计施工一体化的方式,采用“装配式建筑+BIM应用+绿色建筑”的建筑新科技、新理念,打造的江苏省首个“住建部绿色校园示范工程”和“住建部绿色科技示范项目”。同时,该项目还承担国家科技部“6.4装配式工业化建筑高效施工关键技术示范”等四项十三五课题,致力于打造绿色校园、百年建筑、国家一流的优质精品工程。
项目有教学楼、宿舍楼、图文楼、体育馆(对外开放)、音乐厅(对外开放)等11栋单体,为全预制装配式结构,单体预制率最高超过50%,预制装配率超60%。校区地上8层(最高),地下1层(局部夹层),建筑高度30.4m(最高)。其中,教学楼、学生宿舍、师公寓采用全预制装配式框架结构体系,预制部位包括预制柱、叠合梁、叠合楼板(含屋面板)和预制楼梯;音乐厅和体育馆采用“梁柱节点钢套筒+大跨度型钢梁+叠合板、钢筋桁架楼承板”组合结构体系;墙体采用ALC轻质隔墙,全面实现保温一体化和墙面免抹灰。
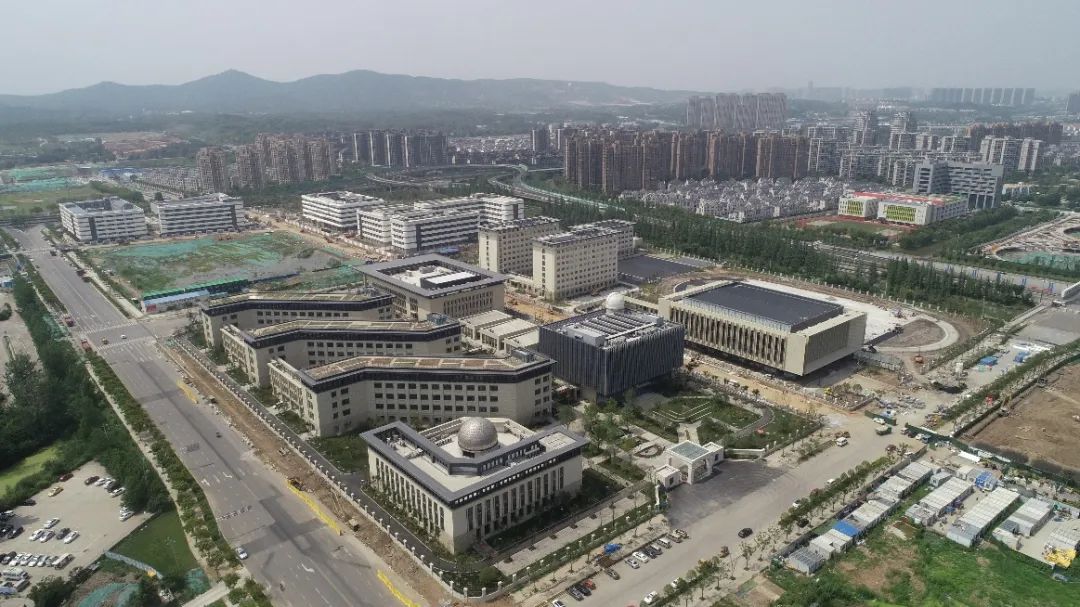
针对教学楼、教师公寓等建筑,创新设计实施全装配式混凝土结构体系,突破传统部分预制、部分现浇的设计方法,从正负零开始采用预制构件,解决预制和现浇混用的装配问题,建立以预制装配为核心的混凝土结构建筑全装配设计体系。
通过设计轴压比控制、连接加强设计技术、结构形式布置规则和抗震性能设计技术,实现全装配式混凝土结构体系。
突破常规,从一层开始大批量采用预制构件,减少钢筋翻样加工、满堂架支模体系搭设和模板翻样加工等工序,缩短工期;减少首层构件现浇施工模板、混凝土、水等资源使用。同时,工业化的建造方式将大部分湿作业转入工厂,有效减少有害气体及污水排放,降低施工粉尘及噪声污染,降低固体垃圾排放,有利于环境保护;明显降低工人的劳动强度和安全事故发生率;提高建造速度,提升建造质量,确保安全文明施工效率。
创新设计:从首层开始,全部预制
对于预制梁柱构件之间连接部位后浇节点钢筋碰撞问题,创新应用梁柱钢筋大直径、大间距、少根数设计技术,保证钢筋连接刚度,实现梁、柱钢筋有效协同,提高建造效率。
预制柱细部展示
梁柱节点效果
叠合梁吊装效果
核心区箍筋绑扎效果
通过钢筋等强代换、钢筋套筒连接、墩头锚连接等技术措施,解决节点连接位置钢筋繁杂,有效减少了吊装过程中构件间预留钢筋的碰撞冲突,避免梁上部钢筋弯折,减小锚固长度,节省钢材使用量,降低施工难度,实现高效装配,加快施工进度。
针对常规水平板出筋导致生产装配效率较低难题,创新采用叠合板不出筋设计方法,便于模具高效安放,提高叠合板生产效率;针对传统叠合楼板分离式连接方式,创新板缝密拼设计方法,规避了传统连接方式下叠合板出筋和板缝预留后浇多产生的生产和装配效率低下等问题。
传统的出筋叠合板
叠合板不出筋、板缝密拼
避免了传统现浇区板带、板缝的后期支模工作,减免工序,缩短工期;提高现场吊装安装效率及准确性;方便工厂进行不出筋叠合板生产。设计阶段通过“标准层不变、开间统一”实现叠合板标准化,方便工厂生产与提高现场施工效率。叠合板不出筋降低开模的难度,提高模具重复利用率,有效降低叠合板生产成本,有利于工业化的推广。
采用组合楼盖创新技术体系,针对音乐厅、体育馆建筑大跨度结构,采用“现浇混凝土柱+梁柱节点钢套筒+大跨度型钢梁+叠合板、楼承板”结构形式。有效发挥混凝土受压、刚度大,钢结构受拉并便于螺栓装配的材料特性,充分利用材料的机械性能,显著减小梁截面尺寸,不仅节省钢材和混凝土用量,同时降低梁高,增加净空同时降低层高;叠合板、楼承板免支模体系,有效降低梁高、减轻自重;减少构件吊装的次数从而节省塔吊用电量,减少预应力梁的模板支设,以及水平板的模板支设,极大提高装配效率和效益。
钢套筒梁柱节点
现场应用效果
通过对结构构件的梳理和归并,构件尺寸标准和模数协调、钢筋尺寸、型号、间距的归并和表转化,提高了预制构件的标准化程度,降低了模具的摊销成本,方便了工厂加工生产和现场施工。
以1#~3#教学楼为例,预制构件(预制柱)标准化程度较高,重复率前三的构件比例均大于90%,单一类型构件个数均在30个以上。
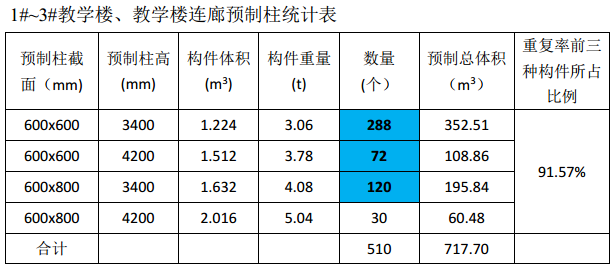
针对叠合板吊装后,梁板面穿筋困难而导致装配施工效率低下,通过对箍筋的优化处理,采用加密区闭口箍、非加密区开口箍的设计方法,兼顾构件工厂制作和现场现浇层穿筋施工,大大降低梁上部钢筋现场安装的难度,提高施工效率。
常规开口箍型叠合梁
加密区闭口箍型叠合梁
非加密区开口箍型叠合梁
非加密区开口箍型叠合梁
构件式的拼装建造设计,使得构件间连接节点成为整个结构的薄弱区,而后期连接区钢筋的有效锚固连接成为结构安全性、整体性的重要保障之一。
常规的弯锚设计,导致节点区钢筋构造更加密集,构件吊装施工难度大、混凝土浇筑不密实,应用梁筋端锚板设计,有效缩短锚固长度,扩大操作空间,简化施工操作流程,保证节点质量。
常规叠合梁端部锚固
主梁底筋端部墩锚板
主次梁搭接部位采用“主梁预留槽口、腰筋贯通+次梁端部锚筋后装”的连接方式,待叠合梁板吊装完成后,次梁端部锚固钢筋通过预埋的直螺纹套筒与梁主筋相连,避免叠合梁吊装过程中主次梁节点钢筋碰撞问题,实现叠合梁的的顺利吊装安装。
主次梁节点
次梁端部构造
预制构件拆分和深化设计阶段,依据梁柱大直径、大间距、少根数技术体系,按照“梁与柱钢筋相互避让、相邻跨梁钢筋相互避让”的布置原则,基于BIM模型进行钢筋碰撞检查和规避,保证构件加工的准确性,确保构件后期高效安装。
梁-柱钢筋避让
梁-梁钢筋避让
梁底钢筋避让实例
项目前期不断推演、完善装配式建筑施工流程,并进行充分准备,根据进度需要提前进行交底与技术指导。项目部在正式装配施工前,就装配式施工过程的节点深化设计、构件合理堆场、构件放线定位、套筒灌浆、及柱端预留钢筋处理等多次商榷,做到装配式施工步骤清晰、合理、简便。
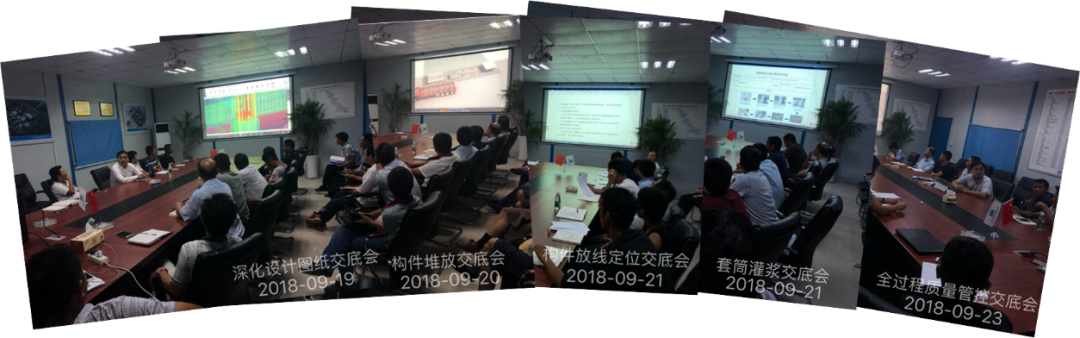
施工过程中,采取科学的“1+6”管理流程,实现了装配式混凝土建造6天/层的速度,回顾、总结装配式施工过程中的人员组织、质量标准、重点难点、方法技巧和工期控制,总结形成了中建科技“装配式标准化施工流程”,填补了施工领域管理标准化表格的空白。
项目持续推进的过程中,针对预制柱下口浆料封堵、套筒灌浆、PC构件吊装等工序,调整施工工序,合理穿插作业、细致周密安排,制定标准化管理流程,装配式标准层(1000㎡,30根PC柱、60根DKL、100块DB;15道工序、7类班组)功效循环上升,工期缩短至6天,其中装配施工工期3天。
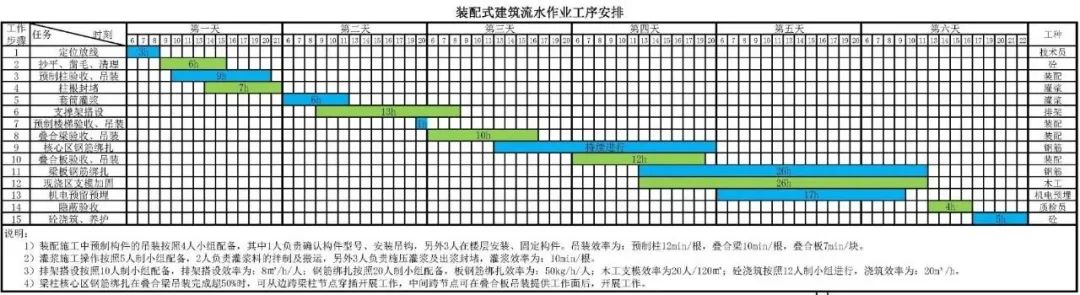
装配式梁柱节点核心区,施工质量尤为重要。核心区钢筋种类繁多,有梁柱构件内钢筋、核心区加密箍筋、腰筋、梁上部钢筋、板面筋等。现浇钢筋的安装由于操作空间狭小、顺序要求严格,施工操作非常困难。面对施工困扰,通过细致分析,创新采用BIM三维交底的形式,动画演示每一根钢筋的安装顺序要求,针对性的解决疑难问题。
可视化交底确保交底的准确性,有助于提高装配施工质量及装配施工效率。
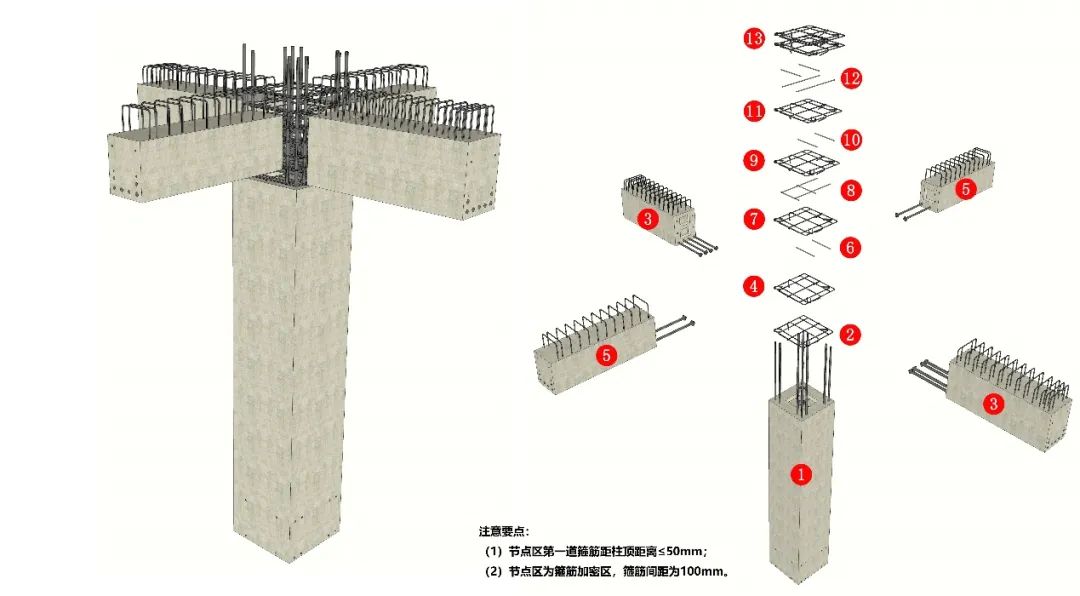
通过充分的技术准备和严格的技术交底,提高操作工人的水平;施工过程中,应用灌浆条件验收表、灌浆令等制式表格,实现标准化管理;全过程旁站、巡视和影响资料记录,确保套筒灌浆的施工质量。
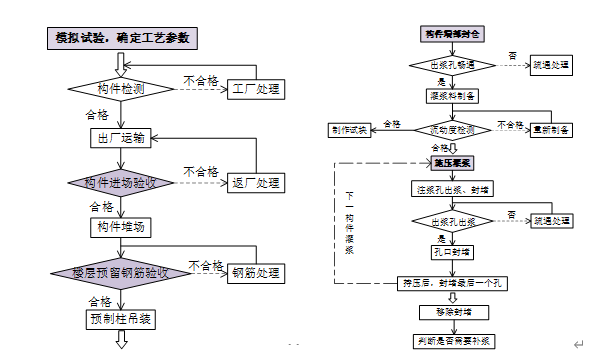
项目在江苏省针对竖向构件的“异常重视和审慎”的环境下,执行2019年关于加强灌浆套筒质量验收的新文件,通过“100%内窥镜观测”、“实体破坏取样剖切29个”的方式,最终检测结果100%合格。装配式质量管控体系、检测方式和执行地方政府规定的措施,在专家论证会上,得到一致认可。