“转自:“
作者:吴耀华 何文汇 王厚昕
中冶建筑研究总院有限公司
中信金属有限公司
含铌低合金钢的耐腐蚀性能
1.1 建筑用金属材料腐蚀的一般情况
耐候钢通过加入耐候元素,会在钢铁材料的表面形成一层50~100 μm厚的致密且附着牢固的氧化膜层。由于这层氧化膜的存在,阻止了大气中氧和水分向钢铁基层渗入,减缓锈蚀向钢铁材料内部发展,从而提高钢材的耐大气腐蚀能力。耐候钢的耐腐蚀性能是碳钢的4~8倍。干湿交替循环有利于保护膜稳定形成,使用耐候钢一般可无须再涂装保护性涂层。
金属材料的耐腐蚀性能,应从两个方面进行分析研究:一是外部腐蚀环境,二是金属材料本体的性能。以沿海地区腐蚀作用的数据为参照,相关研究通过测试得出不同环境腐蚀条件下,多种常用建筑金属材料的腐蚀速率。表1汇总了从几个沿海地区腐蚀试验观察点测试的结果,列出了常用建筑金属材料腐蚀性对比数据。
由表1数据可以看出,环境条件和材料本身的性能共同决定了常用建筑金属材料的维修周期及使用寿命。采用不锈钢、Al、Cu、Zn材质构件可以显著延长使用年限,而通过在钢中加入耐腐蚀性合金元素是提高钢材防腐能力最为直接和现实有效的措施。
表1 常用建筑金属材料腐蚀性比较

1.2 建筑用金属材料腐蚀的一般情况
20世纪中期前,人们开始把铌作为不锈钢的添加元素,提高奥氏体不锈钢的性能。在这之后,铌并没有成为普通碳素钢或低合金钢的一种合金成分。40年代起,人们发现在合金钢中加入铌后力学性能有所提高,从此铌开始成为钢铁材料的一种合金元素,也成为军工产品为提高强度而选用的合金元素。铌对钢材性能的改善主要由细化晶粒引起,它提高了钢材的强度和冲击韧性。此后铌合金化钢材开始在桥梁和建筑钢结构中应用,其耐大气腐蚀的作用也逐渐为人们所认识。
从耐候钢的发展历史看,国际标准ISO 5952∶2005中的附录A(低合金大气腐蚀性的评估指南),是通过各种低合金钢长期(15.5 a)观察测定在不同大气环境下得到的防腐蚀数据,当时采用的钢材样本中并不包括含铌钢,铌对耐大气腐蚀的定量贡献尚难用具体数字表达,但是铌对耐大气腐蚀的有利作用是确定的,且已被试验和工程应用所证实。
耐候钢中含有Cu、P、Cr、Si、Ni、Nb、V、Ti等合金元素,用以改善锈层结构,提高致密度,增强与大气的隔离作用。在上述元素中,铜元素的含量w(Cu)为0.25‰~0.55‰,其作用最大。磷元素也起重要作用,磷元素的含量w(P)为0.08%~0.15%,含磷元素的耐候钢称之为高耐候钢。铜元素与磷元素复合应用的效果更为明显。但磷元素会使钢材的韧性降低,并且恶化钢材的焊接性能,因此只有对耐腐蚀性要求很高时才采用含磷钢。一般焊接结构用耐候钢中磷的含量w(P)≤0.035%,这类钢以Cu-Cr和Cu-Cr-Ni系为主,具有优良的焊接性能和低温韧性。
在国家标准GB/T 4171—2008《耐候结构钢》中,耐候钢化学成分虽没有列入Nb、V、Ti等微量稀土元素的成分,但在附注中说明,为了改善钢的性能可以添加一种或一种以上的微量合金元素:Nb(0.015%~0.060%),V(0.02%~0.12%),Ti(0.02%~0.10%)。若上述元素组合使用时,应至少保证其中一种元素含量达以上规定的下限值,且Nb、V、Ti 3种合金元素的添加总量不应超过0.22%。津西钢厂根据自身铁矿成分并适当添加Nb给出了耐候钢的化学成分配比(表2),充分发挥Nb在耐大气腐蚀中的作用。
表2 津西钢厂耐候H型钢的化学成分(内控标准) %

宝钢在耐火耐候钢研发时,在Q345低合金钢基本成分(0.10%C、0.25%Si、1.0%Mn、0.5%Cr)基础上,进行了单独添加0.02%Nb的钢材(牌号为B490RNQ)的试验研究,这与津西钢厂耐候钢化学成分配比(钢中Nb含量为0.025%~0.035%)相近。通过模拟热带大气环境的湿热试验、周期性浸润腐蚀试验(模拟交替浸入液态腐蚀介质和暴露在空气中)、盐雾试验(模拟咸水或海洋气候腐蚀)以及通过模拟日晒雨淋自然条件下加速老化试验,得到表3—表6所列的试验数据。表中相对腐蚀速率数据表明,含铌耐候钢腐蚀速度大幅降低,其耐腐蚀性能明显优于普通碳钢和低合金结构钢。
表3 湿热试验数据

表4 周期浸润腐蚀试验数据

表5 盐雾试验数据

表6 加速老化试验数据

1.3 耐候指数的计算
在GB/T 4171—2008标准中,提供了评估低合金钢耐大气腐蚀指南(资料性附录D)。为便于应用,Legault和Leckie提出通过化学成分计算耐候指数的计算式,即:

在ASTM相关标准中,定义钢材具有较好的耐大气腐蚀性能时,要求由上述公式计算出的耐候指数应不小于6.0。
对中国标准GB/T 4171—2008、美国耐大气腐蚀结构钢标准(ASTM A588/A588M-15)和ASTM A606/A606M、日本结构用耐候钢标准(JIS G3114—2008、JIS G7102—2000、JIS G3125—2004)、俄罗斯高强度轧制钢材(ΓOCT19281-89)、德、英、法耐大气腐蚀结构钢技术条件等国外材料标准中化学成分的规定值计算出的耐候指数进行比较。结果表明:中国、美国、日本以及津西钢厂内控标准计算出的耐腐蚀指数均在6.0以上,符合耐候钢的要求。而按俄罗斯和德、英、法耐候钢材料标准计算出的耐候指数为4.81~5.13。
对于低合金结构钢(Q345—Q460)、优质碳素钢及碳素结构钢(如20号钢及Q235钢),无论是按材料标准规定的化学成分,还是按材料检验实测的成分计算,耐候指数均在2.0以下,与钢材耐大气腐蚀要求有较大差距,均不能作为耐候钢使用。
根据耐候指数计算式,相关元素中,Cu对耐腐蚀的贡献较大,其次是Ni、Cr、Si、P。从津西钢厂H型钢实际产品的化学成分和内控标准的化学成分分析可知,即使不考虑Nb对耐腐蚀的贡献,其Cu、Ni、Cr、Si、P的含量已能达到耐候指数限值的要求,具有双重保险作用。宝钢试验用耐候耐火钢未含有Cu、Ni、P等成分(或所含的量很小),而主要依靠Nb的添加来提高耐腐蚀性能。这些做法均符合GB/T 4171—2008的规定,即为了进一步改善钢的性能,可添加一种或一种以上微量合金元素。如添加铌元素,其含量w(Nb)=0.015%~0.060%。
表7列出了目前国产的耐候钢腐蚀性能(腐蚀失重率)比较。
表7 耐候钢耐腐蚀性能试验数据比较
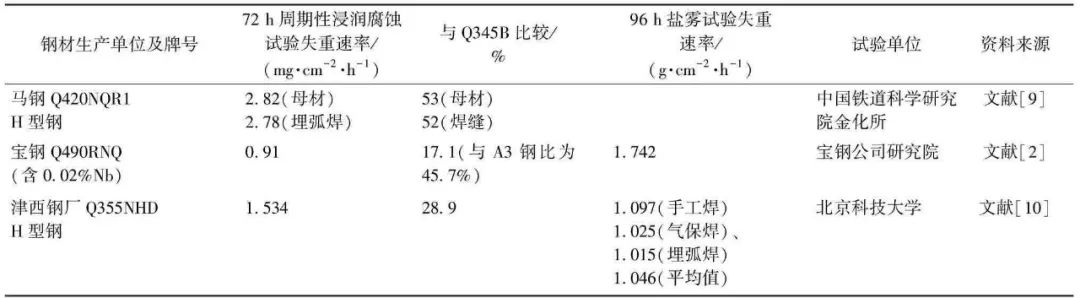
耐候H型钢的力学性能、统计分析及设计强度取值
2.1 轧制H型钢截面材料性能的不均匀性
钢板和型钢的轧制成型工艺表明,当热轧钢板和型材的厚度小时,材料强度较高且塑性和冲击韧性也较好。随厚度增大,其力学性能(如强度、伸长率、冲击吸收能量等)有所降低。由于这种原因,钢板和型钢的力学性能均以厚度分组分别规定。
热轧型钢的不同部位,因辊压轧制变形量不同,力学性能也会产生差别。普通工字钢的轧机只有两个水平轧辊(图1),辊轧成型时,腹板所受压力大于翼缘,翼缘所受压力又与其内侧的斜度有关。由于压力不同,形成组织差异,材料性能随之出现差别,使腹板强度高于翼缘。
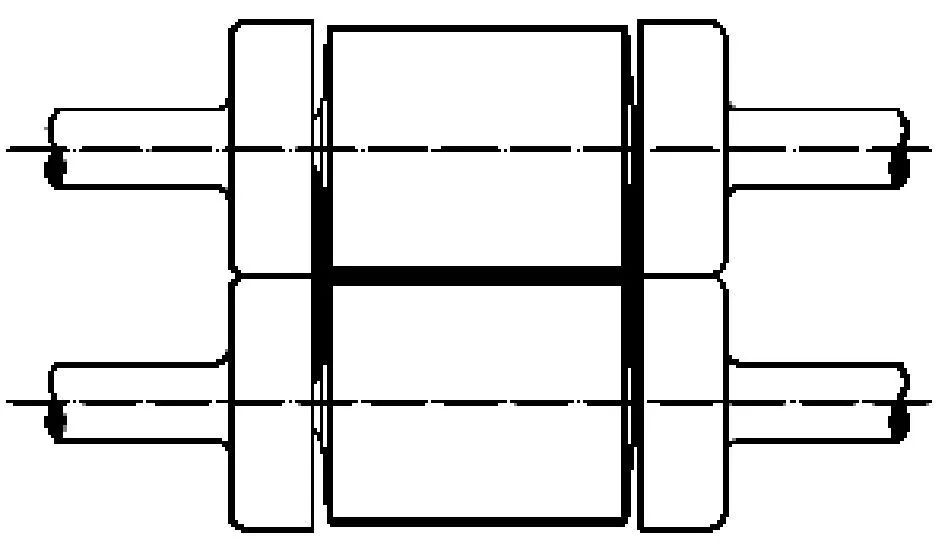
图1 工字钢轧辊
H型钢与普通工字钢不同,不仅翼缘加宽,且翼缘的内侧没有坡度。它是用两个水平轧辊和两个竖向轧辊同时辊压成型的(图2),翼缘和腹板都直接受到压力。由于截面各部位(翼缘、腹板和交接处等)的厚度、轧制变形量和冷却条件不同,翼缘和腹板的材料性能会有不同,且翼缘沿宽度和腹板沿高度各部位之间也有差异。不同的成型工艺和不同的取样位置及测试方法,其材性数据和变化规律也会有些出入。
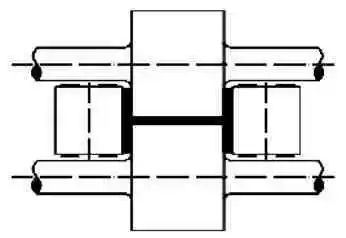
图2 H型钢轧辊
相关研究给出了HN200×200×8×12型钢各部位屈服强度的测试结果,并以曲线形式表示(图3)。翼板的屈服强度值的变化呈W形,翼缘边部的屈服强度最高,翼缘中部与腹板交接处的部位强度也较高,而以翼缘边缘向内1/3宽处的强度为最低。本例中腹板力学性能的变化很小,且在腹板和翼缘交接处的强度较高而中部稍低,这可能与型钢高度较小有关。由于翼缘与腹板各部分的轧制压下量及冷却速度较为接近,性能变化并不明显。
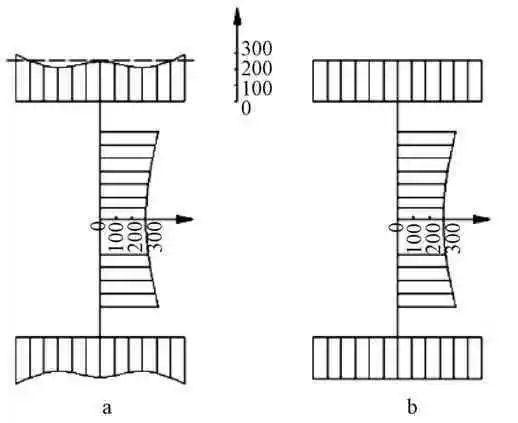
a—实测值;b—简化值。
图3 轧制H型钢屈服强度非均匀分布 MPa
在相关研究中,对H600×200×11×17型钢截面内各部位的力学性能也进行了测定,其屈服强度变化曲线如图4所示。
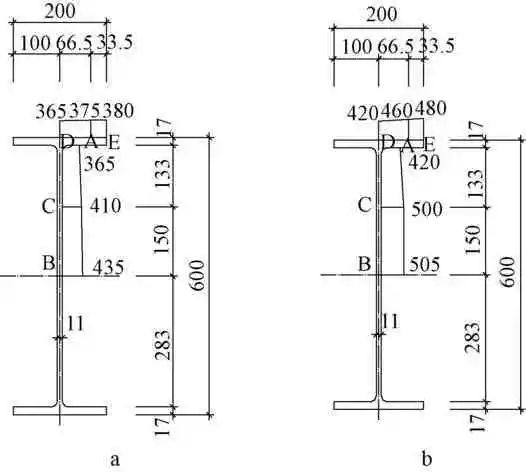
a—H600×200×11×17(Q345B);
b—H600×200×11×17(HSW耐候钢)。
图4 轧制H型钢屈服强度非均匀分布 MPa
本次对津西钢厂生产的两种型号H型钢截面内各部位的力学性能进行了测试,根据测试数据画出H型钢屈服强度变化曲线见图5。
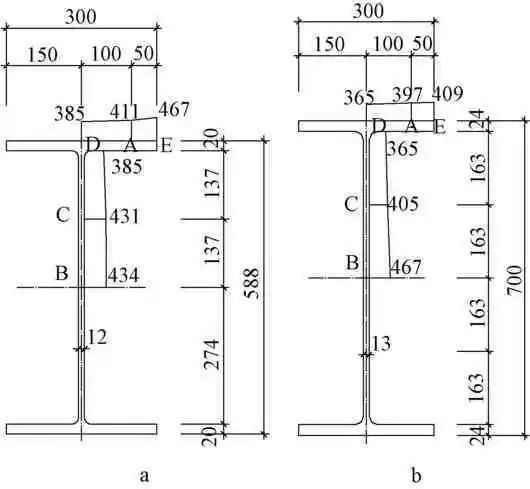
a—HM588×300×12×20;b—HN700×300×13×24。
图5 津西耐候H型钢屈服强度非均匀分布 MPa
以上3组测试数据表明,因轧制和冷却工艺的影响,热轧H型钢截面内屈服强度的分布是不均匀的,腹板的强度普遍比翼缘高些。对于腹板,以中部的强度值为最高,并由中部向翼缘与腹板交接处降低。对于翼缘,以外侧的强度为高,向翼缘中部(翼缘与腹板交接处)呈降低趋势。
由于厚度不同,翼缘和腹板的力学性能会有出入,Young所得的结果是:翼缘的屈服强度在腹板屈服点的76%~98%之间变动。Kennedy和Aly在分析宽翼缘工字钢的统计参数时取翼缘屈服强度为腹板的0.95。有关研究对H450×200×9×14型钢测定表明,翼缘屈服强度平均值约是腹板的90%。
2.2 考虑热轧H型钢截面材性不均匀影响的弹塑性有限元分析
从实测数据看,热轧H型钢截面普遍存在着材料性能的不均匀性,为研讨不均匀性对H型钢构件承载力的影响,采用弹塑性有限元分析方法计算H型钢梁的受弯承载力。以测试获得的各测点力学性能数据为基础,各测点之间的材性按相邻测点的线性变化确定。
选用本次测试的数据进行有限元计算,并与截面强度分布均匀(截面强度统一取翼缘外伸宽度1/3处的强度)的H型钢进行对比。图6、图7所示为Q345耐候H型钢各测点的位置和强度。由于测试数据量少,离散性又大,考虑到相关文献提到在D点(翼缘与腹板交接处)的强度值降得较多,同时也注意到有些文献中强度测试值变动范围较大,为安全起见,在现有测试值的基础上将D点的强度值适当降低(降低5%~9%),见图6、图7(括号内为测试值)。
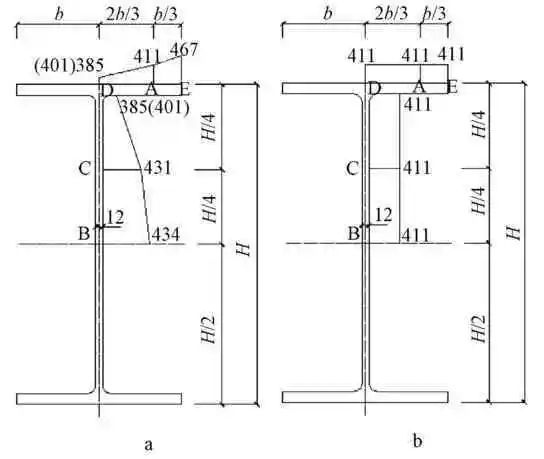
a—截面内屈服强度分布不同;b—截面内屈服强度相同。
图6 型钢HM588×300×12×20截面强度分布 MPa
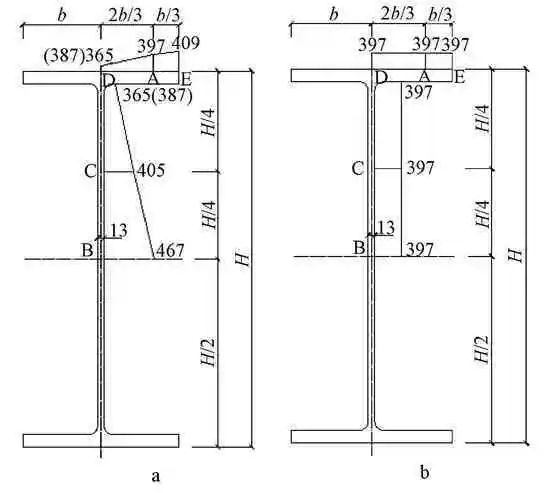
a—截面内屈服强度分布不同;b—截面内屈服强度相同。
图7 型钢HN700×300×13×24截面强度分布 MPa
表8、表9列出了Q345耐候H型钢各部位力学性能,其中屈服强度(fy)和抗拉强度(fu)为试验测定值,弹性应变(εy)由屈服强度及钢的弹性模量(统一取E=2.05×105 MPa)计算得出。εst为屈服平台段应变。此后钢材进入应变强化阶段,当达到极限应变εu时,试件产生局部缩颈而断裂。在性能不均匀的构件截面中,应变值的大小对应力重分布有重要作用。表8、表9应变值的取值是参照文献确定的,这些数据是根据不同强度建筑钢材拉伸曲线经统计分析得出的。
表8 HM588×300×12×20型钢梁材性参数
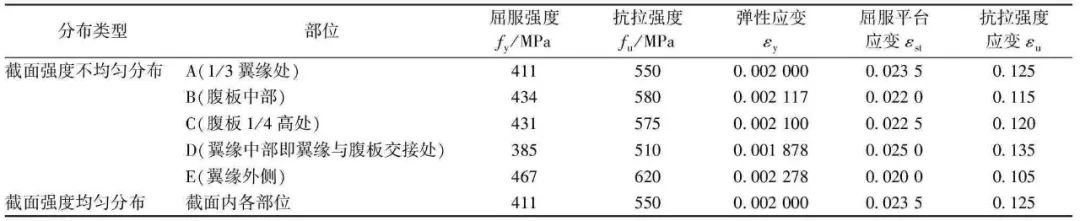
表9 HN700×300×13×24型钢梁材性参数
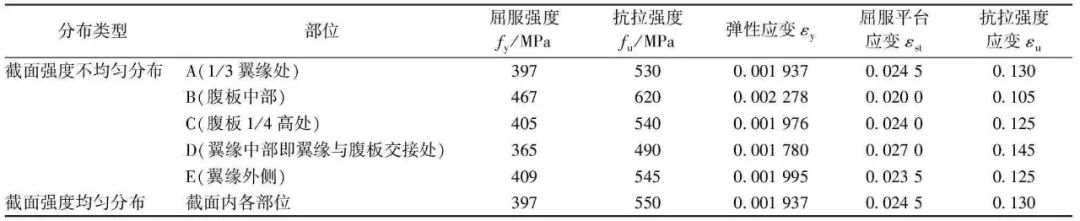
简支梁的受力简图见图8,有限元模型见图9。该简支梁跨度为6 m,在1/3跨和2/3跨处各施加一个荷载为P的集中力。梁用壳单元模拟,梁截面按图9建立,各单元的材料属性按表8、表9设定。
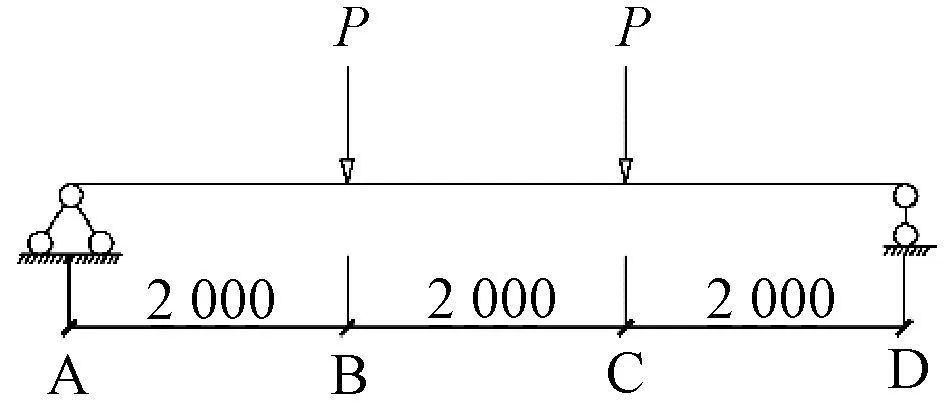
图8 简支梁受力简图
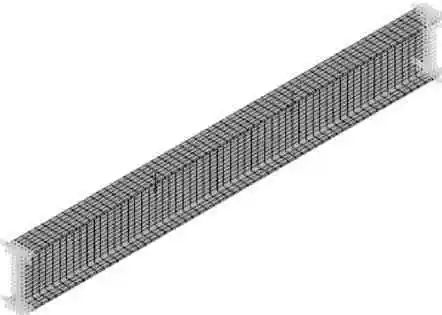
图9 简支梁有限元模型
在简支梁跨中施加的集中力P按荷载步逐级增大。有限元计算完成后,提取跨中截面梁下翼缘中心处节点各个荷载步的竖向位移,绘出荷载-位移曲线,见图10、图11。从图中可以看出,当处于弹性阶段时,2条曲线是重合一致的。当集中荷载施加到1 100 kN时,进入应变硬化阶段,截面屈服强度分布不同的试件产生的挠度为23 mm,比强度均同的试件(挠度16 mm)大。当集中荷载施加到1 200 kN时,HN700×300×13×24试件的荷载-位移曲线出现拐点,说明此时跨中截面已屈服,且进入应变硬化阶段,截面强度分布不同的试件产生的挠度为33 mm,比强度均匀的试件(26 mm)大。
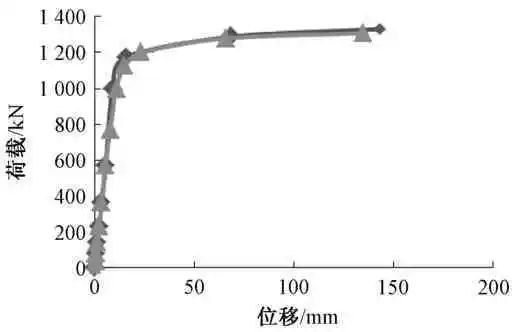

图10 HM588×300×12×20受弯构件的荷载-位移曲线
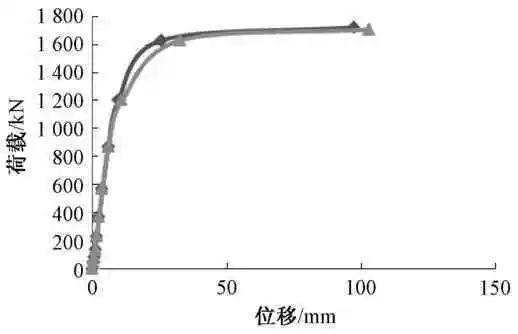

图11 HN700×300×13×24受弯构件的荷载-位移曲线
对强度分布不同的两个试件的荷载-位移曲线比较可知,在硬化初始阶段,位移相同时,截面强度相同的试件能承受的荷载比截面强度分布不同的试件稍大。产生这种情况的原因主要是,截面强度分布不同的试件在翼缘与腹部交接处的强度较低,而此处的正应力和剪应力都比较大,但曲线总体的变化趋势与截面强度相同的试件一致。
拉、压杆的计算模型见图12。该杆件高度为6 m,在杆件顶部施加一个荷载为P的集中力,约束杆件顶部水平向的位移和底部水平及竖向的位移,以此进行杆件受拉强度分析和受压稳定性分析。
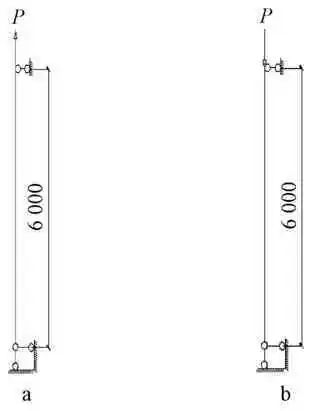
a—拉杆;b—压杆。
图12 拉压杆几何模型
对H型钢拉杆,在顶部施加的集中荷载P按荷载步逐级增大。有限元计算完成后,提取杆件顶部中心处节点的各个荷载步的竖向位移,绘出荷载-位移曲线,见图13、图14。从图中可以看出,当集中荷载施加到6 650 kN时,HN588×300×12×20试件的荷载-位移曲线出现拐点,说明此时拉杆截面已屈服。当集中荷载施加到7 200 kN时,HM700×300×13×24试件的荷载-位移曲线出现拐点,说明此时拉杆已全截面屈服。
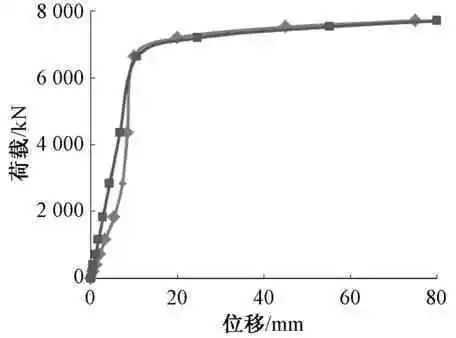

图13 HM588×300×12×20拉杆的荷载-位移曲线
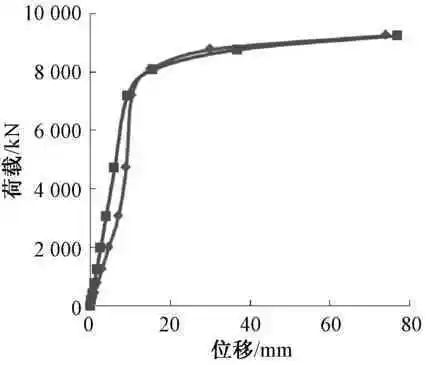

图14 HN700×300×13×24拉杆的荷载-位移曲线
将强度分布不同的两个试件的荷载-位移曲线比较可知,截面强度分布不同的试件在加载起始阶段会产生较大的变形,主要是由于杆件腹板中部的刚度较小,但这种情况对曲线整体的变化趋势没有影响。
对于H型钢压杆,在其1/2高度处水平平面内施加一个6 mm的位移作为压杆的初始几何缺陷(L/1 000,L为杆长),然后释放压杆顶部的竖向位移,并在其顶部施加一个按荷载步逐级增大的集中荷载P。有限元计算完成后,提取杆件1/2高度处受压翼缘中心处节点各个荷载步的侧向位移,做出荷载-位移曲线,见图15、图16。从图中可以看出,当集中荷载施加到6 600 kN时,HN588×300×12×20试件的荷载-位移曲线出现拐点,说明此时杆件受压翼缘已屈服,杆件已失稳。当集中荷载施加到7 150 kN时,HM700×300×13×24试件的荷载-位移曲线出现拐点,说明此时杆件受压翼缘已屈服,杆件已失稳。


图15 HM588×300×12×20压杆的荷载-位移曲线
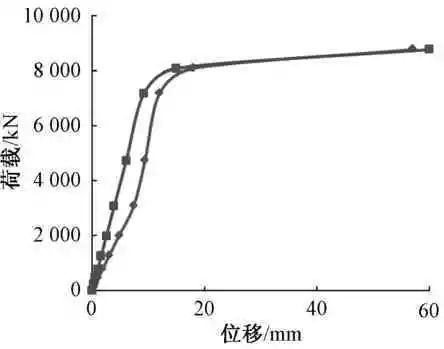

图16 HN700×300×13×24压杆的荷载-位移曲线
将强度分布不同的两个试件的荷载-位移曲线比较可知,在杆件失稳前,位移相同时,截面强度相同的试件能承受的荷载比截面强度分布不同的试件大。产生这种情况的原因主要是,压杆的初始缺陷使其在轴心压力下处于压弯状态,而截面强度分布不同的试件在翼缘与腹板交接处的屈服强度较低,此处的正应力和剪应力却较大,使杆件截面的承载力降低。但杆件进入塑性阶段后,其应力会重新分布,此时强度高的部位会承受更多的荷载,使截面整体的承载力提高,这样截面强度分布不同的两个试件的稳定承载力基本相同。
将受弯构件及轴心受力构件的计算结果比较分析(表10),可得出以下结论:
1)截面内屈服强度分布不同的试件通过实测计算的强度平均值均稍大于1/3翼缘处的强度值(即假定截面内强度相同,按材料检验标准取值)。
2)截面内屈服强度取值不同的受弯构件在弹性阶段的跨中挠度相同,屈服荷载及极限荷载很接近。受弯构件的承载力及刚度受两种强度取值方法的影响很小。
3)截面内屈服强度取值不同的轴心受拉构件的屈服荷载、极限荷载及拉伸变形均相同。轴心受拉构件的承载力及刚度不受两种强度取值方法的影响。
4)截面内屈服强度取值不同的轴心受压构件的失稳荷载相同,失稳时构件的侧移也较为接近。轴心受压构件的稳定承载力及刚度受两种强度取值方法的影响较小。
综上所述,截面强度分布不同的H型钢可取A点(即1/3翼缘宽度处)的屈服强度来表示全截面的整体强度。
表10 承载力及变形计算对比(Q355NHD钢)

注:表中强度平均值由同一截面ΣfiAi/ΣAi计算得出,其中fi为实测值,其余为按相邻实测值线性插值的计算值。
2.3 轧制H型钢的设计强度
在对GB 50017—2003《转自:规范》的修编过程中,曾对热轧H型钢、工槽角钢、焊接H型钢和焊接箱型钢的翼缘及腹板板厚、截面高度及宽度进行测定和分析。根据型钢截面几何尺寸的实际测定数据,热轧型钢与普通轧制钢板一样,成品基本以负公差轧制,有少数型钢产品甚至不能满足GB/T 11263—2005《热轧H型钢和剖分T型钢》对尺寸偏差的要求,已属于不合格产品。热轧H型钢翼缘厚度、腹板厚度、型钢高度、翼缘宽度测定数据统计的直方图如图17—图21。
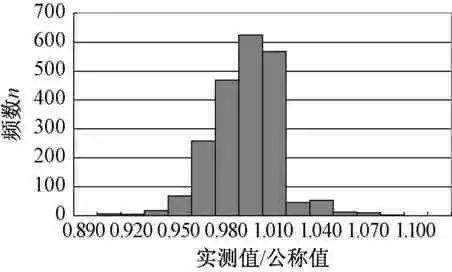
图17 热轧H型钢翼缘厚度(6 mm<t≤16 mm)分布

图18 热轧H型钢翼缘厚度(16 mm<t≤35 mm)分布
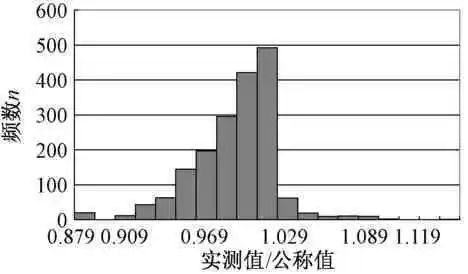
图19 热轧H型钢腹板厚度(6 mm<t≤16 mm)分布
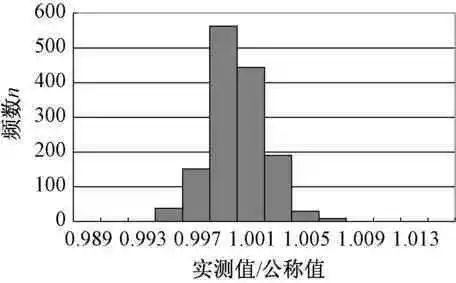
图20 热轧H型钢截面高度分布 mm
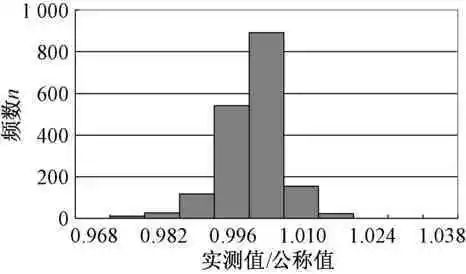
图21 热轧H型钢翼缘宽度分布
由图17—图21可以看出,上述直方图的形态接近对数正态分布。翼缘厚度6<t≤16 mm时,厚度负偏差情况占统计数量的绝大多数。翼缘厚度16 <t≤35 mm时,负偏差的情况有所好转。由于热轧H型钢的腹板比翼缘薄,负偏差对腹板的影响比对翼缘的影响大。H型钢截面高度和翼缘宽度,由于尺寸量级增大,实测值与公称值之比大多数在0.995~1.005之间,分布区间小,数值稳定,统计计算表明其偏差对截面特性的影响很小。
通过热轧H型钢截面面积、惯性矩、抵抗矩、回转半径平均值和标准值的计算,可以得出截面几何特性统计平均值和变异系数如表11所。
表11 热轧H型钢截面几何特性统计参数

对低合金结构钢Q345轧制H型钢的几何尺寸和材料强度进行了数据采集和统计。考虑到钢板与型钢在同牌号同厚度分组时强度取值的一致性,未对轧制型钢作专项分析并规定抗力分项系数,即未对轧制H型钢作出有别于钢板的抗力分项系数和强度设计值。否则同牌号同厚度组的钢板和型钢会出现2个抗力分项系数和强度设计值,给设计带来麻烦。因此对于耐候钢板和型钢,应另行统计分析,不能直接采用普通低合金钢钢板的抗力分项系数。
目前耐候钢板的应用尚少,耐候H型钢尚在试生产阶段,耐候钢和型钢材性数据尚少,相关几何不定性(如厚度、型材几何尺寸等)的数据也少。由于耐候钢与普通低合金钢轧制型钢采用相同的冶炼轧制工艺,一般在同一条生产线上轧制,其几何不定性应相同或相近,可以利用相关文献之表2.5和表2.6作为耐候H型钢的几何不定性参数。
利用普通低合金钢H型钢的材性不定性数据,把相关文献中表3.14 的H型钢材料强度的数据作为耐候H型钢的材性数据(标准值比耐候钢低10 MPa,是偏于安全的)。同时加入津西钢厂试制耐候H型钢的数据,以及本次截面材性不均匀试验和焊接工艺评定试验的材性数据,见表12。
表12 Q355耐候H型钢材料性能不定性统计参数

结构构件计算模式的不定性,主要是指抗力计算所采用的基本假定和计算式精确性等引起的变异性。一般可通过与精确模式的计算结果相比较,或与各种受力类型构件试验结果相比较来确定。由于耐候钢和普通低合金钢的材性相近,在目前尚无热轧耐候H型钢构件试验资料的情况下,耐候钢构件计算模式不定性与普通低合金钢构件计算模式不定性参数取值一致。
关于材性试验方法的影响,如试验加载速度的影响、试验机柔度的影响等均与GB 50017—2017《转自:标准》编制时的取值相同。采用与相关文献中相同的计算方法求得Q355耐候钢(H型钢)的抗力分项系数如下:
厚度6 mm<t≤16 mm,γR=1.128
厚度16 mm<t≤40 mm,γR=1.134
为了与GB 50017—2017中Q345钢相应厚度组设计强度协调匹配,本文建议Q355耐候钢(H型钢)的抗力分项系数取值如下:
厚度6 mm<t≤16 mm,γR=1.183;
厚度16 mm<t≤40 mm,γR=1.169。
Q355耐候钢(H型钢)的抗力分项系数建议取值比统计计算值偏大,由此换算得到的钢材强度设计值偏保守,是安全的。Q355耐候钢(H型钢)强度设计值见表13。
由上述统计和分析比较可知,Q355NH型钢的强度设计值与Q345钢板、型钢的取值相同,这样既方便设计应用,也偏于安全。
表13 Q355耐候钢(H型钢)强度设计值

含铌耐候钢的焊接工艺评定
3.1 焊接工艺评定的一般要求
焊接工艺评定是制订钢结构制作安装工艺规程技术文件的依据,是证明结构工程所采用的焊接工艺能满足结构使用性能要求的技术性文件,也是提供监督管理部门进行开工审批、钢构件工厂制作和现场安装监督管理及交工验收的必备文件。
津西钢厂冶炼、轧制的耐候H型钢(Q355NHD),其微量合金强化元素的类别与一般耐候钢(如GB/T 4171中的Q355GNH)有所不同,增加了铌(Nb)的含量,强度高且塑性好,在国内尚属首次生产和应用。因此,按GB 50661—2011《钢结构焊接规范》的规定,对首次采用的钢材、焊接材料、焊接方法、接头形式、焊接位置、焊后热处理制度以及焊接工艺参数、预热后热措施等各种类型的组合,应在钢结构制作及安装之前进行焊接工艺评定。在钢材研制试生产阶段,可为工程应用时提供焊材品种、焊接参数等技术资料,以便顺利推广应用,这可作为实际工程焊接作业时可参照应用的范例。
本次工艺评定进行了平板对接接头和T形角接接头焊条电弧焊、埋弧焊、富氩气体保护焊,即2类接头形式、3种焊接方法的工艺评定试验工作,可满足含铌耐候钢结构制作和安装的要求。
3.2 手工焊工艺评定
Q355NHD钢手工焊采用的焊条牌号为CHE506NiCrCu(直径为3.2和4.0 mm),由大西洋焊材厂生产。
工艺评定采用钢板T形角接接头、平焊,接头形式和焊接顺序见图22。
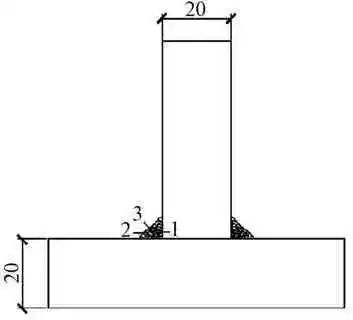
图22 焊接接头形式和焊接顺序
手工焊条电弧焊时,焊接工艺参数见表14。
表14 手工电弧焊工艺参数
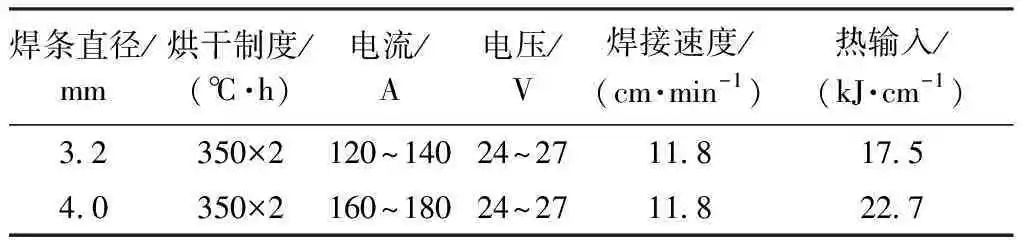
焊后在焊件上截取试片,以与焊接方向相垂直的横截面为试验面,将试验面进行刨、磨、精磨并抛光,采用硝碇水溶液腐蚀后进行宏观金相试验。图23表明宏观观察无缺陷,符合GB 50661—2011的要求。
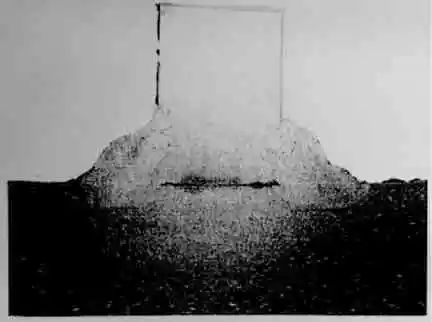
图23 宏观金相照片
对试板采用硝酸酒精溶液腐蚀后进行硬度试验,测得各部位的维氏硬度见表15。
表15 焊接接头各部位的硬度 HV

硬度测定是在试件立板面向下2 mm 的试验线上进行的。熔合区至热影响区相邻试验点之间的间距为1 mm,热影响区第一点距熔合线0. 2 mm。各区域维氏硬度测定值均不大于350 HV,符合GB 50661—2011 标准对于Ⅱ类钢( 标准屈服强度大于295 MPa 且不大于370 MPa 的钢材) 焊接接头硬度值的要求。
焊缝表面经砂轮打磨,以化学浆糊为耦合剂,对工艺评定试板的焊缝进行了100%的超声波探伤。依据GB 50661—2011,未发现超标缺陷,所检焊缝全部合格(贴角焊缝合格标准为二级)。
3.3 气体保护焊工艺评定
Q355NHD钢气体保护焊采用的焊丝牌号为CHW-40CNH,由大西洋焊材公司生产,型号为H08 MnSiCuCrNi Ⅱ,φ1.0。
采用富氩气体保护焊,焊接用气体为CO2(15%)+Ar(85%),焊接位置为平焊,接头形式为T形对接(接头形式及焊接顺序同手工电弧焊,参见图22)。焊接工艺参数见表16,熔敷金属力学性能见表17。
表16 气体保护焊工艺参数

表17 熔敷金属力学性能(实测值)

Ⅰ型焊丝采用CO2气体保护焊时,宜采用小电流焊接(300 A以下),Ⅱ型焊丝采用富氩保护气体,宜采用大、中电流焊接(φ1.2焊丝的焊接电流在250~300 A之间)。
3.4 埋弧焊工艺评定
Q355NHD钢埋弧焊采用的焊丝及焊剂牌号分别为CHW-STH550Ⅲ和CHF101NQ,其力学性能参数见表18。
表18 熔敷金属力学性能
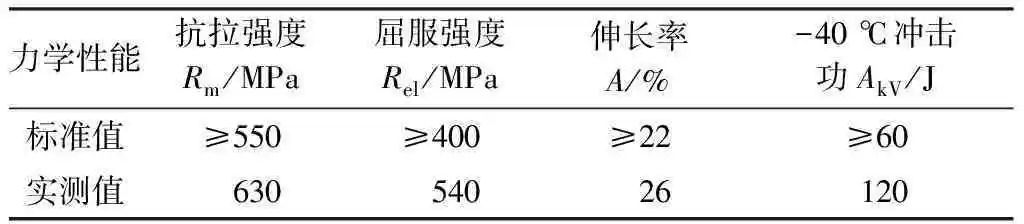
本次工艺评定采用的焊接工艺参数(实际测定值)见表19。
表19 埋弧焊焊接工艺参数

结论
1)津西钢厂生产的Q355NHD耐候H型钢,其内控标准和实际产品的化学成分和力学性能均符合GB/T 4171—2008要求,由化学成分计算得出的耐候指数均符合钢材耐腐蚀性能的要求。
2)经测试和计算分析,H型钢构件的力学性能可按材料检验标准以1/3翼缘宽处的材性试验值代表整个截面的性能,在结构分析中可按均质材料计算。
3)根据对津西钢厂H型钢材料强度的统计分析,考虑材性不定性、几何不定性和试验不定性后计算得出的抗力分项系数统计值比Q345钢统计值小,为了方便设计人员采用,建议偏于安全地取与Q345钢相同。其强度设计值(表13)可供工程设计采用。
4)Q355NHD钢经手工电弧焊、气体保护焊和埋弧焊对接及角接工艺评定,均能满足含铌耐候钢构件制作安装的要求。焊接材料可选用相关焊材厂的产品,焊接工艺参数可参照本次评定试验或相关焊材厂推荐的工艺参数,在构件制作安装前尚应进行工艺评定。
5)应开展耐候钢钢板材性数据的收集和统计分析,尽快得出国产耐候钢板的抗力分项系数和强度设计值,以满足工程设计和应用的要求。
来源:吴耀华,何文汇,王厚昕. 耐候H型钢的材料性能和设计强度取值研究[J]. 钢结构, 2019, 34(2): 15-25.
DOI: 10.13206/j.gjg.201902003